making an electric guitar shim
making an electric guitar shim
Hi everyone. I'm wondering if anyone has any ideas on how to make a decent shim for an electric guitar that I'm refurbishing?
I want a full-size wooden shim that tapers down to zero, as per this article and this item from Stew Mac:
http://www.premierguitar.com/articles/1 ... lnk?page=1
http://www.stewmac.com/Materials_and_Su ... Shims.html
I don't have a belt sander as the article uses. I think I may have come up with a way of doing this with drum sanding attachment for a drill press (which I do have), but that'll need a little experimentation.
So my question is this. Can anyone share any other ways of making these, especially with hand tools? Or any ideas for jigs to get this made accurately?
Thanks in advance.
Bern
I want a full-size wooden shim that tapers down to zero, as per this article and this item from Stew Mac:
http://www.premierguitar.com/articles/1 ... lnk?page=1
http://www.stewmac.com/Materials_and_Su ... Shims.html
I don't have a belt sander as the article uses. I think I may have come up with a way of doing this with drum sanding attachment for a drill press (which I do have), but that'll need a little experimentation.
So my question is this. Can anyone share any other ways of making these, especially with hand tools? Or any ideas for jigs to get this made accurately?
Thanks in advance.
Bern
Re: making an electric guitar shim
Start with a blank of even thickness. Plane into a wedge with a block plane. Finish off on a sanding board. This is how I make the elongate wedge that sits between the neck and fretboard on my Gore style classicals.
Actually that may not work if the shim is really thin as I imagine it will be. You might find something useful here: http://www.seymourduncan.com/forum/show ... -neck-shim
Actually that may not work if the shim is really thin as I imagine it will be. You might find something useful here: http://www.seymourduncan.com/forum/show ... -neck-shim
Martin
Re: making an electric guitar shim
All sorts of ways of doing it. but I really don't believe there is any advantage in the full contact shim.
- Steve.Toscano
- Blackwood
- Posts: 495
- Joined: Thu Feb 07, 2013 11:43 pm
- Location: Port Stephens NSW
Re: making an electric guitar shim
A few options (or a combination).
Hand plane
Hand sand - either block or with sanding board.
Powered hand held sander (small belt or orbital)
Could even do it with a chisel.
Hand plane
Hand sand - either block or with sanding board.
Powered hand held sander (small belt or orbital)
Could even do it with a chisel.
Re: making an electric guitar shim
Stewmac sell them http://www.stewmac.com/Materials_and_Su ... Shims.html But I would probably do as Martin said (or use my belt sander but you don't have one).
Edit: Sorry I should have clicked on your second link.
Edit: Sorry I should have clicked on your second link.
Jeremy D
Re: making an electric guitar shim
Thanks everyone. Interesting to follow one of those links and to see comments arguing for and against full-size shims. Anyway, I'll experiment and I'm sure I'll come up with something.
-
- Blackwood
- Posts: 776
- Joined: Tue Aug 27, 2013 6:36 pm
- Location: North East Victoria
Re: making an electric guitar shim
The hardest part in making a full length shim is to get the angle of the wedge nice and accurate. The angle is easier to set as a gradient, ie ratio of length to height using Pythagorean geometry. For a fine angle, use a long block of wood in order to get an easily measured height to length ratio then work out a way of elevating the block of wood at one end by the measurement needed. I have used double sided tape to hold a shim to lift the block. The shim can then be fine tuned for height by rubbing on sandpaper on a flat surface. One can then use double sided tape to hold the shim blank on the end of the block of wood and sand on a piece of 80grit sandpaper glued to a flat surface. The raising block runs on the flat surface, outside the sandpaper area. Hope that makes sense.
Another way of shimming is with folded pieces of aluminium fly screen at one end of the neck slot. That's quick, the neck screws go through the fly wire easily. There has always been some debate around electric guitar neck joins and the energy transfer that occurs at that junction. Some feel that the bolt on neck causes a sudden loss of energy after the initial attack of the note, then the string drops in volume before it sustains then decays when compared to a dovetail or solid neck. A string attack envelope for a one piece straight through neck gives an initial attack then the string sustains, a dovetail is somewhere in between. After the initial attack from a bolt on neck construction has occurred, the string sustains then decays. The neck join also has some bearing on the rise time of the note. Think Fender sound, with the bolt on neck, the initial attack then decay before sustain gives that more acoustic sound, a Les Paul with dovetail neck gives a more sustaining note right from the word go. The difference between a bolt on and solid neck is even more apparent on a bass. Electric bass builders and the attempts at an acoustic bodied bass often try to achieve the kind of attack decay envelope of an acoustic upright. Solid body straight through necked electric basses sustain forever sometimes it seems, and the acoustic sound can only be emulated with good fretting hand damping of the notes. There have been basses with felt pads which contact the strings at the bridge to try to get an upright bass feel. But don't take my word for it, I'm sure others will chime in(hopefully),do your own tests and then you will know what works for you. Note that the bridge set up has quite a lot to do with the string envelope as well. For example, a Strat with the bridge tight against the body will give a very different sound to the same guitar with the bridge set up for tremolo with the Fender recommended 1/8 inch gap between the body and the back of the bridge. The springs in the tremolo absorb and colour the sound. They also have, in conjunction with the neck timbers, an affect on the string bending action.
Another way of shimming is with folded pieces of aluminium fly screen at one end of the neck slot. That's quick, the neck screws go through the fly wire easily. There has always been some debate around electric guitar neck joins and the energy transfer that occurs at that junction. Some feel that the bolt on neck causes a sudden loss of energy after the initial attack of the note, then the string drops in volume before it sustains then decays when compared to a dovetail or solid neck. A string attack envelope for a one piece straight through neck gives an initial attack then the string sustains, a dovetail is somewhere in between. After the initial attack from a bolt on neck construction has occurred, the string sustains then decays. The neck join also has some bearing on the rise time of the note. Think Fender sound, with the bolt on neck, the initial attack then decay before sustain gives that more acoustic sound, a Les Paul with dovetail neck gives a more sustaining note right from the word go. The difference between a bolt on and solid neck is even more apparent on a bass. Electric bass builders and the attempts at an acoustic bodied bass often try to achieve the kind of attack decay envelope of an acoustic upright. Solid body straight through necked electric basses sustain forever sometimes it seems, and the acoustic sound can only be emulated with good fretting hand damping of the notes. There have been basses with felt pads which contact the strings at the bridge to try to get an upright bass feel. But don't take my word for it, I'm sure others will chime in(hopefully),do your own tests and then you will know what works for you. Note that the bridge set up has quite a lot to do with the string envelope as well. For example, a Strat with the bridge tight against the body will give a very different sound to the same guitar with the bridge set up for tremolo with the Fender recommended 1/8 inch gap between the body and the back of the bridge. The springs in the tremolo absorb and colour the sound. They also have, in conjunction with the neck timbers, an affect on the string bending action.
- Attachments
-
- Untitled.png (8.51 KiB) Viewed 28779 times
"Everything I say on the topic is based solely upon inexperience and assumption!"
Re: making an electric guitar shim
This seems to be a source of great argument amongst players and builders. Dan Erwin is in the full size shim camp.....bernm wrote:Thanks everyone. Interesting to follow one of those links and to see comments arguing for and against full-size shims. Anyway, I'll experiment and I'm sure I'll come up with something.
Martin
-
- Blackwood
- Posts: 776
- Joined: Tue Aug 27, 2013 6:36 pm
- Location: North East Victoria
Re: making an electric guitar shim
The implication of what I posted is that the contact area of the neck joint transfers string energy from the neck into the body. Best way to figure this out is to try an accurately made shim vs a poorly made one, or fly wire, bits of credit card...all the things people use, and compare the results. Some Fenders have a screw which adjusts the neck angle. This doesn't allow the neck to fully contact all surfaces of the mortice that it sits in, not sure if there is any difference from the standard Fender or not. There is a substantial metal insert in the neck for the adjusting screw...Try it and see...http://www2.fender.com/experience/tech- ... icro-tilt/Dan Erwin is in the full size shim camp.....
"Everything I say on the topic is based solely upon inexperience and assumption!"
Re: making an electric guitar shim
This is based on the premise that more contact area = more energy transmission.
I have never seen any experimental or theoretical proof as to why this should be so.
I have never seen any experimental or theoretical proof as to why this should be so.
Re: making an electric guitar shim
By the same argument acoustic guitars with adjustable necks should have less sustain than acoustics with glued/bolted on necks.jeffhigh wrote:This is based on the premise that more contact area = more energy transmission.
I have never seen any experimental or theoretical proof as to why this should be so.
Martin
-
- Blackwood
- Posts: 776
- Joined: Tue Aug 27, 2013 6:36 pm
- Location: North East Victoria
Re: making an electric guitar shim
I am open to whatever the truth is! To quote my original post
. I am not of a strong opinion either way, I posted to stimulate the discussion. Perhaps someone who makes lots of electric guitars can clarify the matter? But it does seem logical to me, that a tight fitting joint will transfer energy better than a loose fitting one.Some (people) feel that the bolt on neck causes a sudden loss of energy after the initial attack of the note
"Everything I say on the topic is based solely upon inexperience and assumption!"
Re: making an electric guitar shim
And they do not have any deficiency in sustain In my experience.kiwigeo wrote:By the same argument acoustic guitars with adjustable necks should have less sustain than acoustics with glued/bolted on necks.jeffhigh wrote:This is based on the premise that more contact area = more energy transmission.
I have never seen any experimental or theoretical proof as to why this should be so.
I would contend that it is not the area of contact, but the quality of contact which makes a difference to sound transmission.
If for example you bedded an Fender style electric neck in a loose pocket with silicon sealant so that there was NO wood to wood contact then I would imagine you would hear a difference.
Consider a modern Stratocaster bridge. its only direct contact with the rest of the guitar is through two knife edges to the posts which are intended to have a minute contact area.
- Trevor Gore
- Blackwood
- Posts: 1629
- Joined: Mon Jun 20, 2011 8:11 pm
Re: making an electric guitar shim
I'm with Jeff on this one. There is no way you can tell what type of (well executed) neck joint a guitar has by listening to it. This one is a tilt neck steel string, though you'd never know that by listening to it. Same with the tilt neck classicals I build.
Fine classical and steel string guitars
Trevor Gore, Luthier. Australian hand made acoustic guitars, classical guitars; custom guitar design and build; guitar design instruction.
Trevor Gore, Luthier. Australian hand made acoustic guitars, classical guitars; custom guitar design and build; guitar design instruction.
-
- Beefwood
- Posts: 24
- Joined: Tue Sep 08, 2015 11:00 pm
Re: making an electric guitar shim
I recently bought a used Fender Baja telecaster and decided to take the neck off to have a look. I found this shim:
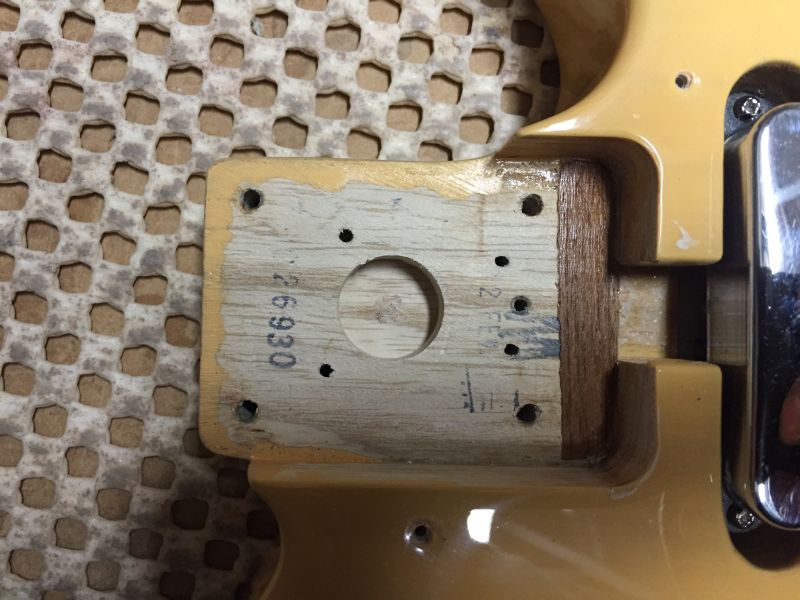
It was only .5mm thick. I didn't think it needed it so I took it out and re-attached the neck and lowered the saddles. I couldn't tell any difference in tone.
Having said that, I've read that having an air gap between the neck and pocket can cause moisture to get into the heel of the neck and cause it to swell a bit resulting in a "rising tongue" at the heel end of the neck. This is obviously not good as it causes string buzz. I don't know if that's true.
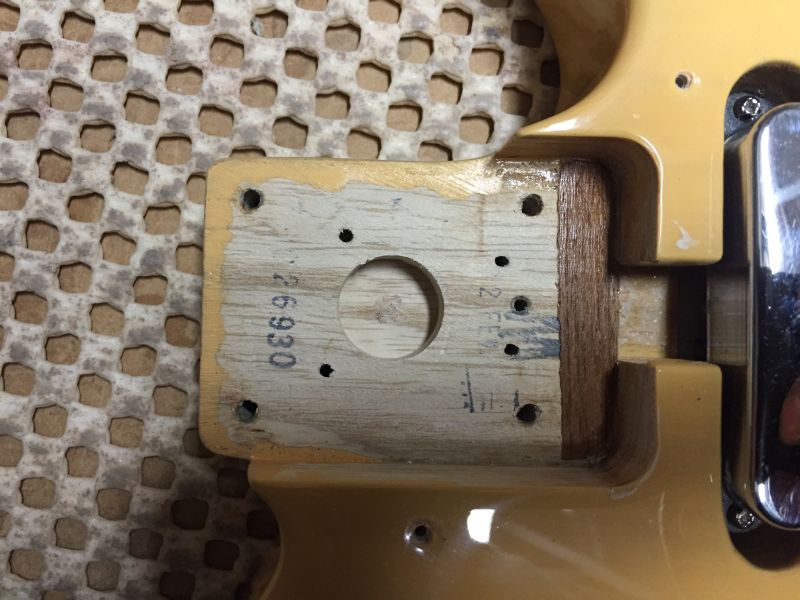
It was only .5mm thick. I didn't think it needed it so I took it out and re-attached the neck and lowered the saddles. I couldn't tell any difference in tone.
Having said that, I've read that having an air gap between the neck and pocket can cause moisture to get into the heel of the neck and cause it to swell a bit resulting in a "rising tongue" at the heel end of the neck. This is obviously not good as it causes string buzz. I don't know if that's true.
Re: making an electric guitar shim
This would have come from Dan Erwin...Blackstar1099 wrote:
Having said that, I've read that having an air gap between the neck and pocket can cause moisture to get into the heel of the neck and cause it to swell a bit resulting in a "rising tongue" at the heel end of the neck. This is obviously not good as it causes string buzz. I don't know if that's true.
Martin
Re: making an electric guitar shim
I don't buy the "air gap between the neck and pocket can cause moisture to get into the heel of the neck" concept.
Re: making an electric guitar shim
On the subject of shims why not use the fiber board it's hard consistent got all the properties you need ,I have only used maple for shims flexible and consistent in most cases .
John ,of way too many things to do.
Re: making an electric guitar shim
Thanks again. I thought I had set things up so that I'd get emails when new posts were added, so I was surprised to come on today and find a bit of discussion.
To be honest, I really have no idea as to whether full-size or smaller shims are better. But I'm going to go with full-size. If anything, it'll be a good mini-project to come up with a way to make a flat, properly angled and consistent shim. I have been out of the workshop for a long time (i.e. years, literally) and I'm dipping my toe in again by restoring two broken instruments in need of love (an old - 80s I think - Vantage electric, and an old and crusty P-bass copy).
Anyway, re: the shim, I'm pretty sure I have a method worked out, similar to what someone posted about sanding a blank with one end slightly elevated.
To be honest, I really have no idea as to whether full-size or smaller shims are better. But I'm going to go with full-size. If anything, it'll be a good mini-project to come up with a way to make a flat, properly angled and consistent shim. I have been out of the workshop for a long time (i.e. years, literally) and I'm dipping my toe in again by restoring two broken instruments in need of love (an old - 80s I think - Vantage electric, and an old and crusty P-bass copy).
Anyway, re: the shim, I'm pretty sure I have a method worked out, similar to what someone posted about sanding a blank with one end slightly elevated.
-
- Blackwood
- Posts: 184
- Joined: Wed Jul 24, 2013 1:51 pm
Re: making an electric guitar shim
I use a piece of brass bar .015" - .025" thick by about !/2" wide across the back of the pocket to get the neck angle right if necessary. Ive seen bits of cigarette packet, sandpaper, credit card etc etc. Never really noticed a difference in tone or sustain.
It is my belief that good compression in the screw down neck joint is the determining factor. Eg if you have a weak crappy neck plate as found on most screw down electrics on nice and tight and digging down into the body on the corners does affect the tone. A nice thick slab of stainless pulled up pretty firm will help things along no end.
It is my belief that good compression in the screw down neck joint is the determining factor. Eg if you have a weak crappy neck plate as found on most screw down electrics on nice and tight and digging down into the body on the corners does affect the tone. A nice thick slab of stainless pulled up pretty firm will help things along no end.
Re: making an electric guitar shim
I have seen cardboard, brass wood. I measured using FFT software no tone difference when changing them to wood.
I make full size shims using 0.6 mm thick jarrah veneer glued like plywood to stop them cracking.
Depending on angle 2 to 4 pieces. Assuming 3 layers are used I do the following.
1 full size, piece, then 2/3 of a sheet 1/3. After clamping and glueing, I trim to shape of the pocket and drill the screw holes.
Then I drop them in this jig and use a sanding block to get it flat on the angled side.
I set the screw in the jig to set the ange, the hinge is a piece of pipe, but a bolt or dowel would work, the pic shows it opened more than I have needed
I make full size shims using 0.6 mm thick jarrah veneer glued like plywood to stop them cracking.
Depending on angle 2 to 4 pieces. Assuming 3 layers are used I do the following.
1 full size, piece, then 2/3 of a sheet 1/3. After clamping and glueing, I trim to shape of the pocket and drill the screw holes.
Then I drop them in this jig and use a sanding block to get it flat on the angled side.
I set the screw in the jig to set the ange, the hinge is a piece of pipe, but a bolt or dowel would work, the pic shows it opened more than I have needed
Re: making an electric guitar shim
Thanks Martin
This is the 3rd one I have made because I loan them and don't get them back.
I should have mentioned the underside has a block glued to it that the screw goes into into,
This is the 3rd one I have made because I loan them and don't get them back.
I should have mentioned the underside has a block glued to it that the screw goes into into,
Who is online
Users browsing this forum: Google, RodC and 42 guests